BALCO Enhances its Material Management with a Digital Ash Control Tower
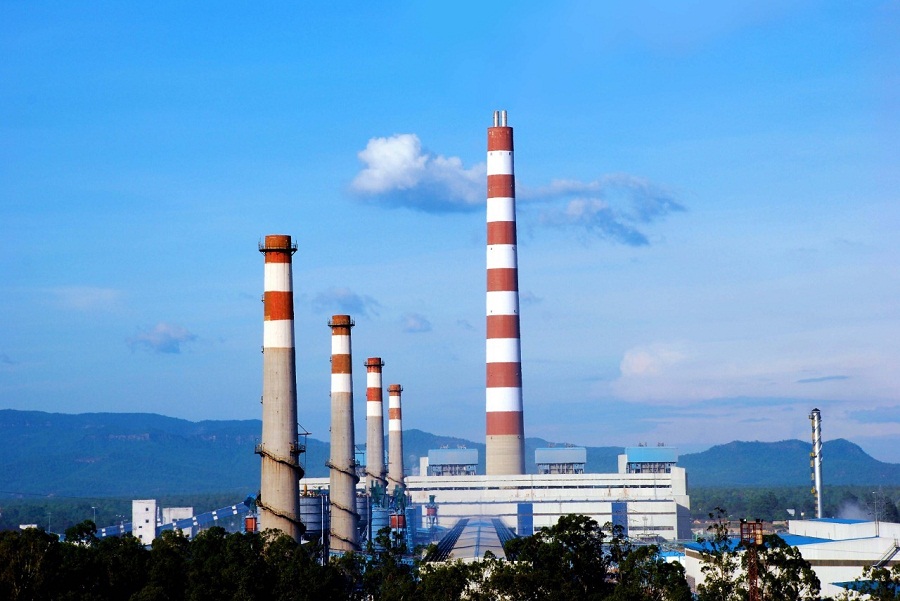
Balconagar. Bharat Aluminium Company Limited (BALCO), India’s iconic aluminium producer and a part of Vedanta Aluminium, has introduced a digital Ash Control Tower, an innovative solution aimed at revolutionizing its vast ash management network. This high-end technology with real-time artificial intelligence (AI) based monitoring plays a pivotal role in strengthening the robust and sustainable management of ash handling fleet while simultaneously bolstering the safety around the operations.
Fly ash is a by-product of thermal power generation with application in diverse sectors such as brick manufacturing, road construction, infrastructure projects, and agriculture. Supply of fly ash to various industries is a part of the company’s circular economy agenda. BALCO, by partnering with various industries has explored avenues for sustainable utilization of the ash, significantly contributing to reduction of carbon emissions and energy, as well as water conservation. In FY24 alone, BALCO supplied more than 4 million metric tonnes of fly ash to support these sectors. These efforts have culminated in a remarkable 141% ash utilization, highlighting the company’s commitment to maximizing resource efficiency and environmental sustainability.
The Ash Control Tower (ACT) offers real time monitoring to ensure strict adherence to ash management guidelines and streamlines the transportation of ash. The technology facilitates a strong network for hassle-free movement of vehicles, bolstering road safety and traffic management. The geofencing system supplemented with cameras enables end-to-end communication that powers real-time AI-based Video Telematics. Video Telematics uses sensors to provide visibility into driver behavior, and it is often used as part of driver safety and risk management programs.
The 24×7 monitoring system is equipped with Advanced Driver Assistance System (ADAS), which improves the safety of the fleet in-charges by detecting and generating alerts for blind spots around the vehicle. This fusion of technology reduces the need for manual checks on the movement and position of the vehicles. Moreover, the comprehensive analytical overview offered by the ACT helps in analyzing the potential risk zones, enabling proactive decision-making while enhancing the preparedness capabilities of patrolling squads.

Speaking about how digitalization is at the core of operations in BALCO, Rajesh Kumar, CEO & Director of BALCO, said, “BALCO has proactively adopted innovative and targeted digital solutions to realize our vision of operational excellence and sustainable aluminium production. Our digital interventions across diverse operational areas have been crucial in improving efficiency across functions while enhancing our safety culture.”
Digitalization has been an integral part of BALCO’s operations offering a comprehensive analytical overview of the operations:
-The Finished Goods Tower and Coal Control Tower facilitates a 24×7 live monitoring dashboard that offers real-time GPS tracking and speed monitoring, ensuring seamless operations round the clock.
-Integration of AI-driven Advanced Driver Assistance Systems (ADAS) and Driver Monitoring Systems (DMS) in internal vehicular operations enhances road safety.
-BALCO houses T-Pulse Health, Safety, Security and Environment (HSSE) Monitoring System for ensuring fulfilment of crucial safety protocols, through a network of cameras using most comprehensive AI models, tracking ongoing activity inside the plant in real time.
-The company has Augmented and Virtual Reality Training Centres, Video Analytics, Sustainability Mobile App, E-learning courses, and Digitalization of Workforce Connectivity to enhance leading indicators in safety practices.
-The Centralized Security Operations Centre (CSOC) in the plant leverages digital intelligence and data insights for better decision-making in security, traffic & road safety, and supply chain security functions.
-Real-time data monitoring, facilitated by end-to-end digital dashboards, including projects like the Hot Spot Detection System at coal yard that uses thermal inspection to ensure strict adherence to safety.
-Use of LED logo projectors in the plant, designed to illuminate safety signs on floors, ensuring clear and prominent display of safety messages in low-light conditions, especially in areas with dust accumulation and high vehicular traffic.